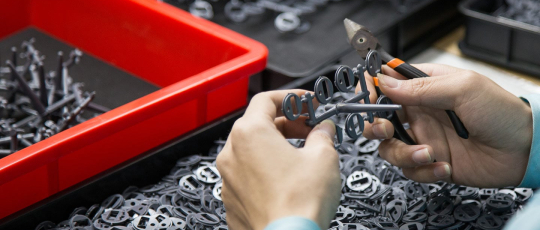
Designing plastic injection molded parts takes a special skill set. It requires knowing the plastic injection molding process including how the material behaves and how the plastic injection molding machine works. Even if you aren’t an plastic injection molding engineer or expert, there are four things to keep in mind when designing your plastic part.
Plastic loves to warp.
To understand plastic, you need to review how plastic parts are formed through injection molding.
First, the plastic injection molding machine heats the plastic material to a liquid state. It then is injected into a mold while it is hot and liquid. However, as soon as the molten plastic particles touch the cold wall of the injection mold, it begins to cool immediately.
Since the entire mold needs to be filled, more plastic is stuffed inside the mold under tons of pressure. This forces the plastic into the mold’s position, which the plastic does not really want to be in.
At this point, the plastic material cures and solidifies, giving it no chance to move. Do not be mistaken though: this plastic has tension; it is just frozen in place, waiting for a chance to relax.
Think about a time you might have put a plastic lid or a plastic food container into the dishwasher to clean it. It probably came out warped after the dry cycle. Why is that?
Inside the dishwasher, the plastic is heated and brought closer to its melting point, but not to the point of melting. However, the heat from the wash cycle gives the material a bit of leeway to loosen up. The plastic releases a bit of its tension by a fraction. When this happens, the plastic warps.
When designing a plastic part, consider questions like these:
- Could environmental influences heat up your plastic part?
- Will you have electronics inside the plastic part?
- Are you taking into account any heat that is generated from those components?
- Could your end-user do something with the product that might heat it up? For example, leave it in a car on a hot day or, as aforementioned, stuff it in the dishwasher?
If you answered yes to any of these questions, make sure you pick a material that can withstand high temperatures or consider reinforcing the design with enough support walls to hold the outside plastic in place. In addition, review your design with your plastic injection molding manufacturer to get their expert opinion if there is any risk of warpage to the plastic.
Plastic loves to sink and shrink.
Here’s a little physics lesson: hot objects expand and cold objects contract.
This concept applies to plastic components.
When a plastic part is being formed in an injection molding machine, the walls of the part mold (or cavity) get covered in plastic first. This means that the walls harden first. At the same time, the core of the mold continues to be filled with hot, liquid plastic which is completely expanded.
As the core cools down, it contracts. In doing so, the hardened outside areas of the mold are pulled toward the core.
The different cooling rates of the various areas of the plastic part most inevitably creates sink marks.
The thicker an area means it takes longer to cool. Therefore, the walls on your plastic parts should be as evenly thin in all areas as much as possible.
How thin you can go is decided by the material that you use. For example, ABS plastic should have a wall thickness of around 2mm to 3mm.
However, there is an exception for interior walls that support other walls (also known as ribs). These particular walls should be around 50 - 75% of the thickness of the main outside wall.
For instance, if your part has a housing thickness of 2.5mm, then all ribs should have a thickness of around 1.8mm.
Plastic can have weak areas.
Let’s assume you have a component that is a plastic ring. When the ring is created inside a plastic injection molding machine, plastic is inserted at one end of the ring. The material flows into the ring, divides, and runs along both sides. It then meets on the other end where the material touches and rejoins with itself.
However, there is one problem with this touch. On its way through the ring, the liquid material has already started cooling down, curing ever so slightly. This means that the touch area cannot be mixed perfectly because each side has already started to cure.
This particular spot is called a weld mark.
There are two issues to be aware of with weld marks. The first issue is that weld marks are visible which reduces the aesthetics of the piece.
The second, more major issue is that the weld line is weaker than the rest of the plastic part. If any pressure is applied to the part, it most likely will crack at the weld mark.
Work with an experienced manufacturer to ensure any critical or problematic areas are addressed
Most weld marks are preventable. Work with an experienced manufacturer to ensure any critical or problematic areas are addressed and weld marks are avoided.
Plastic is very impressionable.
As plastic flows through the mold in the injection molding machine, if a design has a variety of thin and thick walls or sharp corners, there can be turbulence as the plastic fills these spaces. This turbulence can cause flow marks.
Another way that flow marks appear is the plastic injection molding machine settings. The gate size and the injection pressure are parameters that can be adjusted to minimize flow lines.
However, if your design is not optimized for the injection molding process, no amount of equipment adjustment can prevent flow marks. Avoid a design that’s not manufacturing ready by partnering with a manufacturer that provides DFM (design for manufacturing) as a service.
Depending on your product’s design, your plastic parts can give the impression of whether it’s a quality product or not.
Warpage, sink marks, weld marks and flow lines are just an introduction to the types of issues that can arise when molding plastic parts.
By working with an experienced manufacturer, you can prevent these common plastic injection defects to give your product a strong first impression.