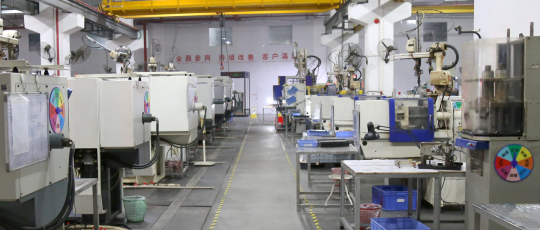
When you start out designing a new product, one of the first questions you may have is, how much will it cost to make it? Determining the total production costs upfront allows you to plan with obtaining funds or tweaking your product so that it meets your target sell price.
Factors that affect Manufacturing Costs
There are a variety of factors that affect the cost during the different phases involved with building a product. Therefore, there is no special manufacturing cost formula to easily come up with the cost of production.
Before a golden sample is even created, funds will need to be put toward product design, market research, non-recurring engineering (NRE), and more.
Once the product is produced on a large scale, there are additional costs involved with shipping, warehousing, and distributing the product.
What about the phase in between - how much will the production costs be?
There are two types of costs to review when looking at how much it will cost to manufacture and build your product.
The first type is made up of flexible costs (also known as variable costs). Variable costs in manufacturing mean that your choices and planning can have a direct impact on what the end cost will be.
The second group of manufacturing cost influencers are fixed – these come at a standard price that cannot be changed with negotiation or selections made.
Variable Costs in Electronics Manufacturing
The first variable cost that influences your total manufacturing cost is the manufacturability of your product.
How DFM affects Production Costs
The product will need to be put together in an efficient way that is manageable with the technology. One part of the production process is to ensure the product design fits within equipment and assembly capabilities.
This approach for preparing the product before it reaches mass production is called DFM (design for manufacturing). DFM considers the guidelines and restrictions of manufacturing when designing a product.
If the product’s assembly drawing never took DFM into account, the production facility will modify your design to fit their manufacturing processes. This additional work on the factory’s end will add an extra cost to your total build. It may also compromise the quality of the finished product.
Keep your production costs down and maintain control over your product design by creating a ready-to-manufacture design package before you reach the production phase.
Keep your production costs down and maintain control over your product design by creating a ready-to-manufacture design package before you reach the production phase.
How your Materials affect your Product Costs
Another item that impacts total manufacturing costs that are within your control are the product’s materials.
Your bill of materials (BOM) lists the subcomponents, parts, and raw materials needed to create your product.
You have the final say of what constructs the product. Therefore, ensure that the BOM is in line with your product’s target selling price while leaving some margin for profit.
If the total materials cost is higher than you originally planned, then either adjust the line items within the BOM or make sacrifices on certain features or materials so that you can stay at your target selling price point.
Other Variable Factors that affect your Production Costs
Additional items that affect how much it will cost to manufacture your product include:
- total production quantity
- your timeline
- packaging choices
How Volume affects Cost of Production
The number of units produced in a production run will affect the total cost. A larger volume will mean a cheaper cost per unit.
Review your estimated quantity requirements over 12 to 24 months and see if it would make financial sense to do a larger production run all at once versus less-frequent, smaller runs over time.
Your production volume quantity is a classic risk versus reward decision that you must make based on the needs of your business.
How Production Timeline affects Manufacturing Costs
Your timeline will also affect your production costs.
A seasonal product that is only manufactured at certain times of the year typically won’t receive any preferential treatment from a production facility.
On the other hand, if a factory knows you will be a steady ongoing customer with weekly production needs, you most likely will see a price break as a way to ensure their lines stay at capacity.
How Packaging affects Product Costs
Packaging your product is the last step within the manufacturing phase before it can be shipped and distributed out into the world.
You have two choices with how it is packaged: bulk packaging or retail packaging. Both options will affect the total cost.
Bulk packaging is the cheapest option but not the prettiest.
Retail packaging makes your product stand out on the shelf against your competitors.
Your choices within package shape, paper stock, ink choices, and extra sales inserts will need to be factored into the cost of manufacturing.
Beyond creating the packaging, it will then need to be assembled with the product.
If your packaging is quite intricate, you could see this reflected in the manufacturing and assembly costs.
The manufacturability of your product, BOM, total quantity, timeline, and final packaging of your product all play a factor in the cost to build it.
These areas are considered variable costs since they are based on your decisions and can be adjusted to fit your target price point.
The manufacturability of your product, BOM, total quantity, timeline, and final packaging of your product all play a factor in the cost to build it.
Fixed Costs in Manufacturing an Electronic Device
There are additional items to consider that affect manufacturing costs which you have less control over. These costs are set by the third party providing the service and typically are more difficult to negotiate.
Manufacturing Overhead Costs that affect Production Costs
The first item that adds to the manufacturing cost is a factory’s margin.
The factory adds an additional amount to their base production cost in order to cover their overhead costs. The factory overhead is an indirect cost that still needs to be accounted for.
Manufacturing overhead costs can encompass a variety of categories such as:
- labor cost
- factory equipment
- supplies
- quality control
This additional margin may not be shown as an individual line-item within your total cost however it will certainly be taken into account as part of the markup on the production cost.
A factory will also need to prepare physical space, equipment and tools, and train workers to be ready to produce your product on a large scale. The time and effort to prepare these items is known as the production setup.
Similar to factory overhead costs, production setup may not be a line-item on your invoice but it is another factor that determines the total markup.
Compliance Fees that affect Production Costs
A final item that affects how much it will cost to manufacture your product are compliance testing fees.
Every country is different, however most require your product to pass compliance testing before it is sold within that country.
Each country has their own set of requirements; some overlap with other governments’ product compliance rules while some do not.
Therefore, it is important to be aware of all the different compliance regulations your product must meet and the costs associated with each individual certificate. Compliance lab testing costs will vary depending on the certification.
Quick Review of Production Costs
There are many different factors that affect how much it costs to manufacture an electronic product.
The total manufacturing cost formula is:
Variable Costs + Fixed Costs = Total Cost of Production
It can be difficult to calculate total manufacturing cost before speaking with your manufacturer.
Therefore, it’s best to involve your manufacturer as early on in the process as possible. They can help support you in areas where you have direct influence to help you meet your final target price point.
Your variable costs are influenced by your product design decisions and your product development strategy.
While the fixed costs are items beyond your control and are set by the vendor supplying the service.
With forethought and planning, your estimated production costs can be aligned with your target unit cost.
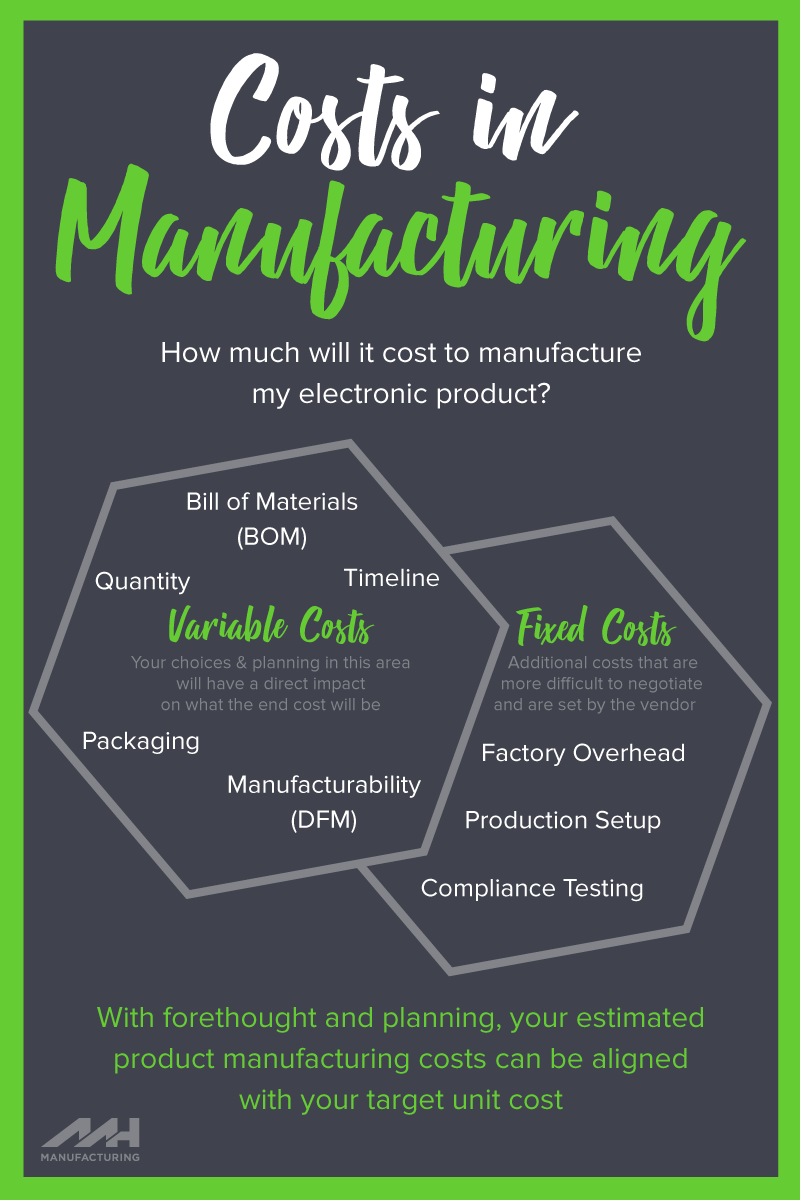